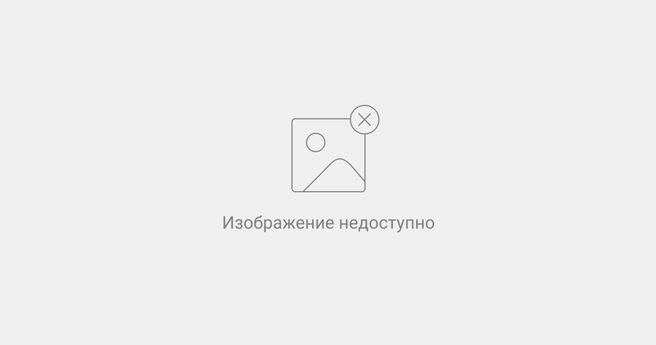
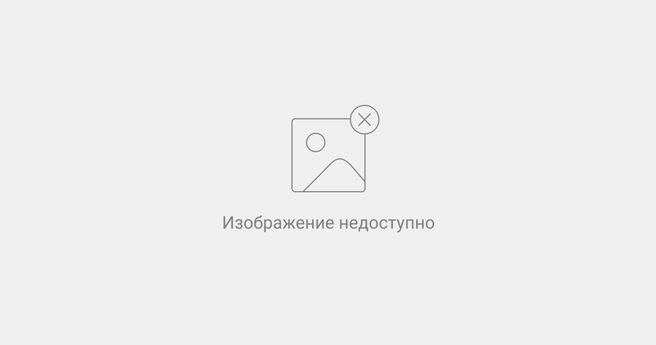
В 2011 году ОАО «Челябинский электрометаллургический комбинат» отметило свой 80-летний юбилей. О том, почему этот год стал для предприятия знаменательным, каких результатов удалось достичь, на какие высоты подняться и какие проблемы разрешить – в интервью с главным технологом ЧЭМК Дмитрием Ракитиным.
«Вернув ЧЭМК былую мощность, мы занялись его модернизацией»
– Дмитрий Игоревич, каким аспектам развития предприятия было уделено наибольшее внимание в минувшем году?
– Выделить только одно направление невозможно, поскольку параллельно улучшения шли по разным параметрам – от экологии и автоматизации производства до внедрения на нашей площадке инновационных технологий.
Стоит понимать, что комбинат модернизировался и строился непрерывно – в 30-х, 50-х, 60-х годах и в конце 70-х. В 80-е годы произошел некоторый застой в целом в стране, и на нашем комбинате в частности. В 90-е мы выживали, в 2000-х занимались восстановлением того, что было упущено десятилетием ранее. Именно тогда вновь начались ремонты, обдуманная поставка сырья и оборудования, и предприятие уверенно встало на ноги. А последние три-четыре года ЧЭМК реально приступил к изменению своей промышленной политики в области развития. Мы обратили свои взоры на опыт зарубежных партнеров. Раньше наша страна была не просто за железным политическим, но и за плотным технологическим занавесом. Все промышленные предприятия СССР развивались на основе обмена опыта друг с другом. Иностранцы же смотрели на развитие и наше, и друг друга, невзирая на коммерческую тайну. Я не скажу, что предприятия в СССР были отсталыми, но ряд тенденций на них все же серьезно упускался. К примеру, экология в СССР во внимание не принималась, тогда как в Европе решение экологических вопросов считалось приоритетным.
Не менее серьезное значение для нас имеют и вопросы, связанные с внедрением на предприятии автоматизированных систем. Их решение важно по двум причинам. С одной стороны, человеческий ресурс не из дешевых, и о нем нужно заботиться, создавая нормальные условия для работы и уделяя внимание социальной составляющей. С другой же, наличие человека на производстве влечет за собой человеческий фактор, в той или иной степени влияющий на качество нашей продукции. И чем длиннее эта цепочка, тем негативнее может оказаться конечный результат. Это прекрасно видно на опыте японских автомобилестроительных предприятий: чем меньше задействовано людей, тем более качественные машины сходят с конвейера.
Огромное внимание мы стали уделять тому, что напрямую влияет на выживание предприятия в современных экономических условиях, – внедрению безотходных технологий. Это возврат пыли в производственный процесс, переработка отсевов, освоение выпуска других материалов попутной продукции с высокими потребительскими свойствами и с удовлетворительной рентабельностью. Все это, а также переход на новые виды сырья и выпуск дополнительных видов продукции, повышение ее качества, внедрение на комбинате систем менеджмента качества и многое другое позволяют ЧЭМК сохранять на рынке стабильно хорошую репутацию и регулярно выплачивать зарплату. Активно внедрять эти элементы на предприятии мы начали где-то с середины 2000-х, а год минувший стал в развитии комбината, пожалуй, одним из самых насыщенных.
Отказ от решения экологических проблем приводит к закрытию предприятий
– Дмитрий Игоревич, почему изменения на ЧЭМК начались именно с экологической составляющей?
– Если предприятие, тем более черной металлургии, находится в центре города и оказывает вредное воздействие на окружающую среду, жителей и собственных работников, то вариантов развития событий немного: либо изменяется политика предприятия, и оно начинает уделять внимание решению экологических вопросов, либо оно закрывается. И обсуждать качество продукции и ее себестоимость в таком случае становится бесполезным. Если есть значительные выбросы, то давление власти и общественности приведет к вынужденной остановке любого завода.
– И какие же экологические проблемы уже удалось решить?
– Почти полностью были сокращены выбросы в двух наших цехах – №7 и №8. Там с помощью нашего партнера – южноафриканской компании Gore – были спроектированы и запущены в эксплуатацию системы газоочистных сооружений с эффективностью улавливания загрязняющих веществ до 99,7 процента. Этот показатель значительно лучше экологических норм, утвержденных как в России, так и в большинстве стран мира.
В начале следующего года будет введено в эксплуатацию третье газоочистное сооружение, в котором мы учитываем заранее все, что пришлось изменить в уже действующих газоочистках. То есть здесь мы пошли по уже отработанному пути, вновь используя мембранные фильтры для рукавов, которые гарантируют на выходе чистый воздух с содержанием вредных веществ не более 5 мг на кубометр. И это при существующем стандарте в России и за границей в 10–20 мг! Эти фильтры из спецткани нам поставляет тоже южноафриканский партнер – компания Gore. А для того, чтобы обеспыленные продукты горения максимально разбавлялись воздухом, мы устанавливаем трубы высотой не менее 80 метров.
Без внедрения инноваций не выжить
– Дмитрий Игоревич, расскажите, пожалуйста, об инновационных направлениях предприятия, но уже не в экологии, а в производстве.
– Побывав в первом десятилетии текущего века в Америке, наши руководители убедились, что ферросплавные печи, выплавляющие ферросилиций, могут работать не только на коксе, но и на угле. Для нас это было в диковинку, потому что вся ферросплавная отрасль черной металлургии прошлого века в России была ориентирована на использование кокса. В 21 веке цены на кокс выросли, и назрела острая необходимость перехода на новое, более дешевое природное сырье – каменный уголь. Но, как позже выяснилось, сменить его непросто: для работы на новом сырье не подходят существующие конструкции печи и газоочистки. Несколько месяцев наши специалисты подбирали технологии, режимы, детально прорабатывали производственный процесс, и в конце концов нам удалось почти полностью заменить коксовый орешек каменным углем. К сожалению, часть оборудования под резко возросшими температурами выстоять не смогла, перестали справляться газоочистки. Взамен мы построили новые газоочистные сооружения и приступили к реконструкции различных агрегатов с учетом опыта зарубежных стран.
– Но что же здесь инновационного?
– Использование в производстве каменного угля привело к тому, что отработанные газы стали горячими. Поначалу мы приняли решение снизить их температуру, построив газоочистки с новыми системами охлаждения. Потом задумались, нельзя ли тепло и энергию ферросплавного газа превращать в тепло для человека в виде пара и горячей воды. Оказалось, что подобный опыт внедрен в Скандинавии, Исландии и ряде других стран, которые считают не только центы, но и гигакалории попутной энергии.
Изучив опыт сторонних компаний, начиная от Китая и заканчивая всей западной Европой, год назад мы привлекли к сотрудничеству две крупные норвежские проектные фирмы. Они разработали базовый проект, который ляжет в основу строительства на комбинате целого ряда принципиально новых агрегатов не только для собственного обеспечения теплом, но и части города. То есть в рамках программы, рассчитанной до 2020 года, мы планируем выйти в общую систему городского отопления. Планируется 12 наших печей оборудовать котлами-утилизаторами, так называемыми бойлерами, которые будут превращать энергию горячих ферросплавных газов в тепло. Намерены опробовать на ЧЭМК различные варианты переработки этой энергии – в острый пар, тепло, горячую воду, каждый из которых сейчас детально просчитываем. Это и есть наша инновация – в России ни на одной ферросплавной печи котлы-утилизаторы еще не установлены.
Использование отходов производства приумножает прибыль
– Дмитрий Игоревич, расскажите, пожалуйста, о еще одном пути к промышленному прогрессу ЧЭМК – внедрению безотходных технологий.
– Понятно, что отходы образуются всегда и везде, но вопрос в том, как к ним относиться. В сельском хозяйстве, например, безотходные технологии используются не первый век. В металлургии долгие годы ситуация обстояла иначе. Выпуская товарную продукцию, практически каждое предприятие металлургической отрасли в нашей стране возводило на своей территории огромные горы шлаковых отвалов, отсевов сырья и прочих отходов. Нередко отходов получалось больше, чем основной продукции. Сейчас ни возросшие цены на землю, ни экономическая, ни экологическая ситуация, ни другие аспекты производства ферросплавов не позволяют вести себя таким образом.
Как известно, предприятия группы ЧЭМК занимаются переработкой кварцитов, из которых производят необходимый для выплавки стали ферросилиций. Одним из побочных продуктов производства ферросилиция является микрокремнезем, который ранее считался лишь вредным выбросом в атмосферу, теперь же перешел в разряд ценнейших продуктов. Мы улавливаем этот микрокремнезем и упаковываем для последующей вторичной переработки. К примеру, его можно использовать как суперактивную добавку в бетон, способную изменять химический состав и физическое строение цементного камня, улучшая его структурно-механические свойства. С его помощью получается коррозионностойкий, морозостойкий, водонепроницаемый, долговечный материал небывалой прочности и такой пластичности, жидкотекучести, что бетонную смесь можно поднять бетононасосом на требуемую высоту укладки. Для приобретения бетоном этих свойств достаточно 10 процентов микрокремнезема. Именно из такого бетона строят высотные здания во всем мире.
Использовать микрокремнезем в строительстве в том виде, в котором его получают при улавливании дымов, достаточно проблематично: материал очень легкий и мелкий, по размеру частиц относящийся к ультрадисперсным, его сложно как транспортировать, так и добавлять в бетон и другие строительные растворы. Предварительно эту пыль нужно уплотнить, не изменив свойств частиц. Наши специалисты разработали технические варианты по уплотнению микрокремнезема, под которые было заказано необходимое оборудование. Его поставка запланирована на конец текущего года, значит, уже в начале следующего мы получим первую партию готового к употреблению модификатора. Кстати, с помощью этого оборудования производство ферросилиция перейдёт в разряд малоотходных технологий.
– Дмитрий Игоревич, есть ли еще какие-нибудь отходы комбината, которые в ближайшем будущем перейдут в разряд ценных материалов?
– Помимо микрокремнезема в нашем производстве образуются пыли хромовых и марганцевых печей. В том виде, в котором мы их собираем, они никому не нужны, хотя некоторый интерес со стороны других плавильных предприятий все-таки есть. Но эти пыли интересны нам, поскольку в хромовой пыли есть хром, а в марганцевой пыли, соответственно, марганец. Без специальной технологии вовлечь эту пыль обратно в производство невозможно. Понятно, что разработки в этой области есть, это, к примеру, технология окомкования разнообразными способами – начиная от агломерации и окатывания до брикетирования и прочих нестандартных решений. Однако к пыли хромовых и марганцевых нашего производства они еще ни разу широко не применялись. А наше предприятие этим вопросом занялось вплотную. К сотрудничеству пригласили специалистов из Екатеринбурга, которые разработали под нас технологию брикетирования и изготовили основное оборудование.
За 2011 год мы прошли немалую часть стандартной процедуры внедрения нового производства: разработали проект и технологию, приступили к его детальному проектированию, изготовили основное оборудование и определились с тем, какие агрегаты следует приобрести дополнительно. Но чтобы не потерять время и узнать, как разные технологии брикетирования влияют на качество конечной продукции, мы стали поставлять нашу пыль нескольким организациям, у которых есть схожее проектируемому нами оборудованию. Мы оцениваем различные результаты, принимаем участие в корректировке технологий, меняем связующие материалы… Несмотря на то, что при этом мы несем чрезмерные затраты на транспортировку сырья и готовых материалов и оплату услуг этих компаний, мы готовы на это идти, ведь все это помогает нам определить дальнейший путь развития технологии брикетирования на ЧЭМК.
Покупать коксовый орешек невыгодно? Значит, будем производить его самостоятельно
– В начале беседы вы отметили, что полностью отказаться от использования коксового орешка все же не удалось. Необходимый объем этого материала предприятия группы ЧЭМК по-прежнему закупают, или же было найдено иное решение?
– Чтобы сделать комбинаты группы ЧЭМК полностью независимыми от рыночных колебаний цен на кокс и всевозможных перебоев с его поставками от сторонних предприятий, было решено запустить собственное производство кокса на модернизированных австралийской компанией ретортных печах. Такой цех будет запущен на одном из структурных подразделений группы – Юргинском ферросплавном заводе в Кемеровской области. Австралийская технология позволит снизить стоимость потребляемого при ферросплавном производстве кокса в несколько раз. При этом она будет отвечать всем мировым экологическим требованиям. Сейчас идет обсуждение нюансов дальнейшего сотрудничества.
«Мы готовы обнародовать реальный уровень выбросов на ЧЭМК»
– Летом по инициативе областного правительства возникло движение по установке на предприятиях Южного Урала оборудования, позволяющего контролировать количество производимых выбросов. Планируется, что данные мониторинга будут размещаться в онлайн-режиме на одном из интернет-ресурсов и будут доступны всем желающим. Как на это требование губернатора Михаила Юревича откликнулся электрометаллургический комбинат?
– Установка таких пылемеров на ЧЭМК была запланирована еще давно, в рамках реализуемой предприятием экологической программы, рассчитанной до 2015 года. Поэтому на постановление областного правительства мы откликнулись, пожалуй, первыми.
Эти системы мониторинга очень сложные, поэтому некоторое время назад мы обратились за помощью к коллегам из Норвегии, Германии, Франции и других стран, где подобное оборудование эксплуатируется на протяжении многих лет. Европейцы поделились с нами информацией о различных фирмах-производителях и их продукции, которую наши специалисты пристально изучили. К вниманию была принята аппаратура таких ведущих мировых корпораций, как Sick MAINAK, Durag, PCME, Goyen и SIMATEK.
Как обычно, мы занялись поиском универсального оборудования, позволяющего удовлетворить все наши требования – по стоимости, условиям эксплуатации, надежности, реальности показываемых значений и прочему, и чтобы оборудование при этом было сертифицировано в России. Определившись с выбором, мы отправили наш проект на утверждение в областное правительство, дабы после не пришлось что-либо переделывать. Мы готовы заказать пылемеры сразу, как только администрация примет решение.
Модернизация ждет и электродное производство
– Все, что вы рассказывали, так или иначе связано с производством не основных видов продукции. Но можно ли говорить о модернизации производственных мощностей конкретно в электродном и ферросплавном производстве?
– Ферросплавное производство, я уже рассказывал, мы модернизируем по многим причинам – подошли сроки капремонта, который мы делаем с элементами модернизации. То есть внедряем технические решения, позволяющие работать на новом виде сырья, снижающие долю ручного труда в обслуживании печей и повышающие надежность оборудования. Все это ведет к снижению себестоимости и увеличению объемов выпускаемой продукции.
В модернизации же электродного производства все не так просто. У наших иностранных коллег есть очень емкая фраза, определяющая их отношение к электродному производству. Они называют его черной магией. Эта отрасль очень закрытая, поскольку производители электродной продукции жестко конкурируют на рынке как по цене, так и по качеству продукции. Здесь такого общения и обмена опытом, как среди ферросплавщиков, просто нет. И найти организацию, готовую модернизировать сразу весь электродный комплекс, невозможно. Есть множество предприятий, производящих отдельные элементы оборудования электродного производства, связать которые воедино очень сложно. Замена пресса, смесителя, газоочистки или печи однозначно повлечет за собой смену целой цепочки из оборудования, технологии, сырья и номенклатуры выпускаемых изделий.
На наш взгляд, гораздо целесообразнее, не останавливая существующее производство, где-то рядом на территории нашей площадки разместить экологически безопасное, компактное, современное, инновационное электродное производство. А старое просто закрыть. Таким образом, не приостанавливая работу своих людей и выпуск нашей продукции, можно за раз решить большинство проблем. Модернизация электродного производства назрела давно, и мы сейчас вплотную занимаемся рассмотрением ее различных вариантов.
На правах рекламы.